By Jody Sackett
MIDDLETOWN – The house hides its secrets well.
Driving by it on Kings Highway, you would never realize this house is very different from its neighbors. It is one of only three Unity Homes houses in New Jersey – a high-performance, carbon-neutral home.
“Our energy costs for the year, including charging our two electric vehicles, is zero,” said owner John Burke, who loves living in this remarkable house with his wife Diane.
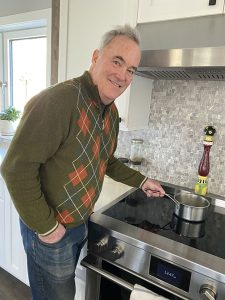
Completed in 2023, the 3,000-square-foot house is made of nearly two dozen prefabricated panels, which were constructed in New Hampshire but assembled on site in Middletown. Panelized homes are known for their efficiency, minimal waste, and cost-effectiveness.
Each panel consists of 18-inch-thick walls incredibly well-insulated with non-toxic cellulose between double layers of Tyvek. The panels are built inside the climate-controlled Unity factory, to avoid expansion and contraction due to temperature and moisture changes. Considering the insulated panels must fit together precisely, it’s not surprising that construction is computerized down to the millimeter, to ensure everything is airtight, “like a thermos!” laughs Diane.
The house is phenomenally airtight – it is 5,000% more airtight than a typical home – to ensure minimal heat loss in winter and a comfortably cool interior during the summer. The design also helps mitigate energy loss due to thermal bridging, the movement of heat toward cold through conducting surfaces. An energy-efficient heat pump replaces conventional gas heating and handles cooling in the summer, too. Fresh air is circulated through the house via an Energy Recovery Ventilation (ERV) system that recaptures 90% of the indoor air temperature from the stale exhaust air and transfers it to the fresh incoming air. The ERV also controls humidity.
Neither system uses any fossil fuels and the house doesn’t even have a gas line. Instead, solar panels provide all the electricity needed to operate everything in the house. John has a cellphone app that displays energy production and usage; they are often producing enough energy to sell back to the grid.
The process of building the house started when, as empty nesters, John and Diane began evaluating downsizing options. The couple are still active – John is an economics professor at Monmouth University and Diane taught yoga classes and was a Rumson environmental commissioner – and wanted to stay in the area. They, along with their three children, have been ardent environmentalists for decades, so a priority was figuring out how to lead a comfortable life with the smallest possible carbon footprint. Research led them to Unity Homes. They visited the other two houses in New Jersey and were suitably impressed.
After purchasing an 11-acre lot in Middletown, the Burkes found their ideal general contractor for this unique project in Tommy Gemallaro of T.K.O. Operations LLC. Although Tommy had never built a Unity high-performance home, he was up for the challenge – and this sure was one.
“I love Unity and I love Tommy,” John said. “He was careful, honest, thoughtful and open-minded. He’s been a builder for 45 years but this was completely different. Tommy called Unity often; they were helpful.”
COVID-19 complicated the design and building process on many levels. The Burkes couldn’t visit the Unity factory due to the pandemic, which made it challenging to choose their house layout, bathroom and lighting fixtures, cabinets and more. Production was affected as supply chains entangled, delays were common, parts and materials were unavailable and prices soared.
But the Burkes persevered. They started with the foundation work. The hilly lot had to be graded so the house could face south and capture the most solar energy. Five feet of concrete was poured to create the foundation. It took about a month to complete the grading and foundation work and then it was time for the next phase.
Seven tractor-trailers arrived from New Hampshire carrying the pre-fab panels. Unity rented a giant crane to assemble it all, a process that took nine days. The panels were fitted together, “like LEGOS,” Diane said, to ensure airtight insulation. Doors and triple-paned windows were pre-installed, along with holes drilled for electrical and plumbing lines to ensure the walls remained hermetically sealed once fitted in place. The panels were bolted to each other, as well as to the foundation and the roof.
The result is a solid, strong dwelling that can withstand hurricanes better than a typical house. Cabinets and fixtures were part of the package deal, shipped with the panels and stored onsite until Gemallaro was ready to install them.
Walking through the home, you realize something is delightfully different: The air smells and feels cleaner. It’s quiet – due to all the insulation, you can’t even hear cars driving on the adjacent busy road. There’s no background noise of heating or air conditioning units going on and off; in fact, the fresh air ceiling vents are barely the size of a smoke detector and indiscernible, too.
“A thunderstorm knocked out our power and we didn’t even know!” John said.
“Because the house is so well insulated, we didn’t hear the thunder and the solar battery kept the lights on and the house powered as usual,” Diane explained.
Lots of unique aspects make this house fascinating. There are LED lights everywhere to reduce the energy draw. Low-VOC paint keeps the air pure. The kitchen has a Fisher-Paykel induction stove which saves energy since it doesn’t heat the cooking surface, only the ingredients – electromagnetic coils move electrons in the pot around, making it more efficient than an ordinary electric stove. Chefs love its responsiveness because the heat turns off immediately like a gas stove; there are no red-hot coils, so you can put your hand right on the burner; it’s easy to clean and cooks fast – a pint of water boiled in about three minutes.
Unity Homes, based in Bensonwood, New Hampshire, offers both custom and packaged house designs. John explained that “clients can customize some or all of the home. There’s lots of flexibility in how the designs can be modified,” he said, “and the company works hard to accommodate whatever layout the customer wants.”
The Burkes customized some of their home design, which added additional costs. In the end, the Unity house package cost about $450,000, but the final price tag, including the grading, foundation construction and finishing work on the interior and exterior of the house, was $1.5 million. Final finishing included installing the drywall, roof, flooring, electrical and plumbing. John ruefully noted that the costs skyrocketed due to COVID, with construction materials hard to find and extra expensive.
The Burkes have now happily lived in their ultra-sustainable dream home for about a year. Since completing construction, they’ve turned their focus to the yard.
The property came with a tennis court, which they converted to a garden. First, they removed all the tennis court asphalt, crushed it up and sold it for reuse in road paving. The soil underneath was unsuitable for a garden and needed to be remediated and restored. On half of the tennis court, they “planted clover as a nitrogen fixer and daikon radishes as aerators to draw minerals back up” into the soil to help restore it, explained Diane. They also used composted food scraps and dead leaves to enhance the soil.
On the other half of the court, they built 18 raised beds and planted 35 different types of fruits, vegetables, herbs, flowers, berries and milkweed. “Our vegetable garden plays a pivotal role in reducing our carbon footprint by replacing store-bought produce with whatever is seasonally available for picking from April through December,” said John. They left the 10-foot-tall tennis court fence in place to keep out deer.
The Burkes have begun landscaping around their home using only native plants to attract pollinators, feed wildlife, ensure biodiversity and provide shelter. “Native species support local wildlife and are crucial for a healthy and stable ecosystem,” Diane explained. “They provide shelter and food for wildlife, need little care or water and protect soil from erosion. Our yard is certified as a wildlife habitat through the National Wildlife Federation.”
This innovative home is a model for the future, proving that a beautiful and comfortable home can be sustainable. “The thought that the sun can provide all our energy needs is both exhilarating and forward-thinking – proof that we are powered by the sun,” Diane said with a smile.
This article originally appeared in the March 14 – 20, 2024 print edition of The Two River Times.